Lock It InWith Spiral Wound LinerTM
Forget about whether to push or pull a liner into place: use Spiral Wound LinerTM, which is produced in the diameter needed for the repair at the exact length and no waste. Many feet of pipe are produced from one reel of material, so the cost of shipping is less than factory-manufactured pipe. Plus, the lining is accomplished within the existing right-of-way and with no coupling worry because the liner is one continuous section.
The Spiral Wound LinerTM system is based upon a special extruded plastic profile. This profile has a smooth inside and a T-ribbed outer surface with interlocking edges. When fed through the winding machine, these edges interlock at two positions, and simultaneously, an injected sealant is introduced that also acts as a friction lubricant during the engagement of the locking mechanisms. While the general “T” configuration remains the same, profiles vary in thickness and weight to produce liners that meet performance criteria and diameters. Each profile is made from Rigid Polyvinyl Chloride (RPVC) and, when used with proven sealants and cements, a liner of the highest integrity is ensured.
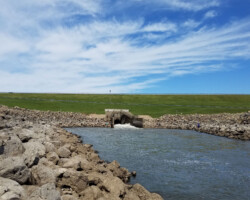
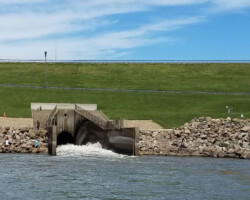
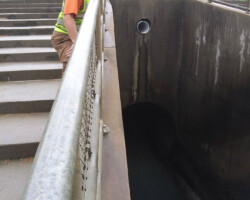
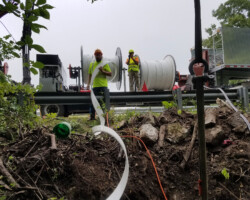
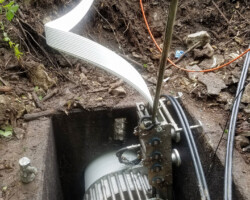
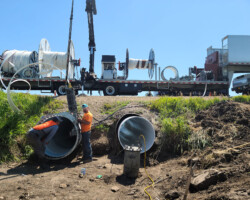
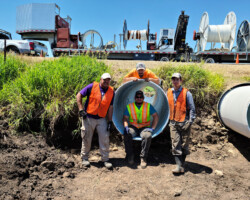
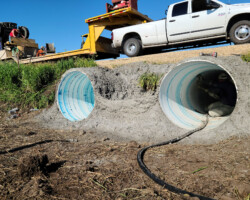
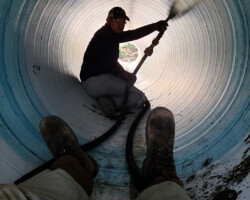
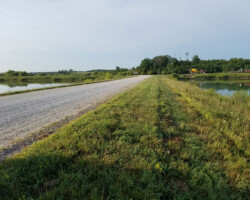
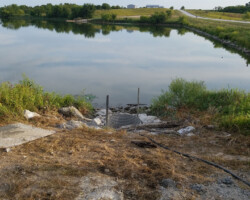
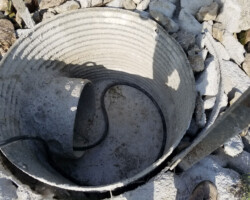
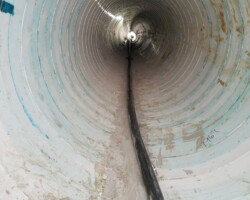
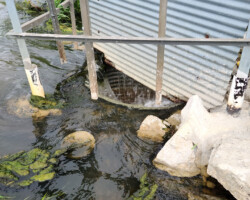
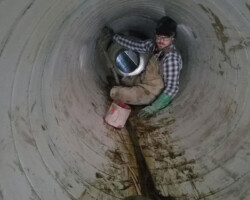
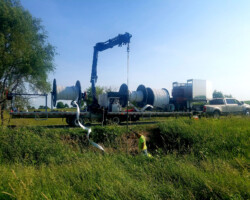
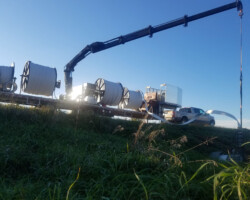
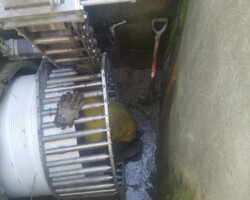
It was so quick with really low impacts on anything.... and saved a lot of money without having to cut the road.
Backed by Exhaustive Quality Testing & Evaluation
- Constructed from PVC. When used with approved sealants and cements, the liner is projected for 80-year performance.
- Various profile dimensions. We can meet exact performance criteria and diameter.
- Due to the friction coefficient of PVC, there is generally no loss of hydraulic flow ability of rehabilitated pipe.
- Manufactured on-site to the exact length needed. No waste and less shipping charges than factory manufactured pipe.
- Less disruption of traffic vs. a complete replacement.
- Meets ASTM F1741 for installation of Machine Spiral Wound PVC Liner and ASTM F1697 specification for PVC liner.
Spiral Wound Liner Sales and Distribution
Contact:
info@spiralwoundliner.com
319-721-5047
Are you using CIPP (cured in place) or slip lining currently?
For your next project, choose SWL.
Why Spiral Wound LinerTM?
IT STARTS WITH THE PELLET.
Our custom-blended compound is sourced from Teknor Apex™, a company founded right here in the USA with global ISO certification. This ensures consistency, pellet after pellet, and aids in flawless extrusion. We are proud to work with Midwest-based, 9001 Quality Management Certified TigerHawk Profiles™ to create the PVC profiles used in our product. Why is this important?
American Made
- Advanced Equipment and Experienced Personnel lead to Impeccable Quality
- Meets ASTM F1741 for standard practice for installation of machine spiral wound PVC liner pipe and ASTM F1697 specification for PVC profile strip for machine spiral wound liner pipe rehabilitation of existing sewers and conduit.
It was so quick with really low impacts on anything.... and saved a lot of money without having to cut the road.
We are so happy we used Richard's liner as compared to others because we went from a 4-6 man crew trying to screw them together in a lot of overdig.
There is not much disruption to traffic. They don't have to close the road or even one lane.
With space limitations, SWL is the exact thing to use.
The smooth lining of the pipe makes it easier to see what is going on inside the pipe vs. having standing water or the bottom of the pipe corroded out.
If you are concerned about your project being cost effective, this is one of the first products you should look at for rehab.
SWL repaired the culvert & the culvert is working properly. Very happy with the product.
An economical solution to extend the life of pipes that have corroded or rusted out without having to tear out the pavement.
Some of the tubes were 25-35 foot deep, so putting a liner in didn't require us to tear up the road, which saved us a lot of money. Also, the water flows through it at a fabulous pace. I'm impressed.
Ours have been installed for about 25 years, and we've not had a bit of trouble. The nice thing is that grout fills in the voids - you don't have to worry about it again.
An economical solution to extend the life of pipes that have corroded or rusted out without having to tear out the pavement.
The primary reason we used SWL was because of failing pipes and rusting out under pavement. It is working exactly the way we intended.
It was amazing how fast and easily it went in and how well it works. We are completely satisfied and don't intend on doing it other way.
How It Works
Spiral Wound LinerTM profile Is extruded onto spools containing as much as 9,000 feet of product. The profile is 5.5 inches wide with heights of ½”; ¾” and 1”. The on-site manufacturing consists of the profile exiting the spool and into a hydraulic winding machine that has a profile-to-pipe transformation cage attached, which produces a liner slightly smaller than the host pipe. The SWL profile-to-liner transformation machine (from a fixed position at an access point) has drive rollers that pull the profile from the spool and around the cage. The winder’s press roller then presses the interlocking edges together; it is at this roller where the sealant is injected.
The continual feeding of the profile through the profile-to-pipe transformation cage results in a continuous spiral wound pipe that traverses through the deteriorated host pipe until it reaches the desired termination point. Subsequently, the annular space is filled with an appropriate grout to fill voids, eliminate infiltration, and gain an additional structural component by bonding the liner to the host pipe.
Profile to Liner Calculation Chart
SWL OD Pipe Size | SWL ID Pipe Size | SWL Ft. | SWL per ft of pipe | Height of profile |
---|---|---|---|---|
16” | 15” | 1 | 9.6 | ½” |
20” | 19” | 1 | 11.47 | ½” |
26” | 25” | 1 | 14.9 | ½” |
32” | 30.4” | 1 | 18.22 | ¾” |
38” | 36.4” | 1 | 21.58 | ¾” |
44” | 42.5” | 1 | 25.13 | ¾” |
48” | 46” | 1 | 27.33 | 1” |
54” | 52” | 1 | 30.77 | 1” |
60” | 58” | 1 | 34.19 | 1” |
66” | 64” | 1 | 37.6 | 1” |
Benefits
Huge Eco-Friendly Benefits
Save thousands of dollars
compared to other rehabilitation methods or replacement. See the advantages and compare the time savings with SWL and Lock It In.
Gallery
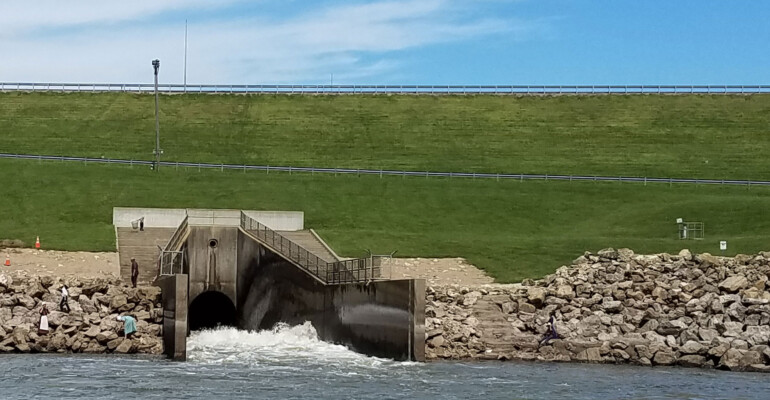
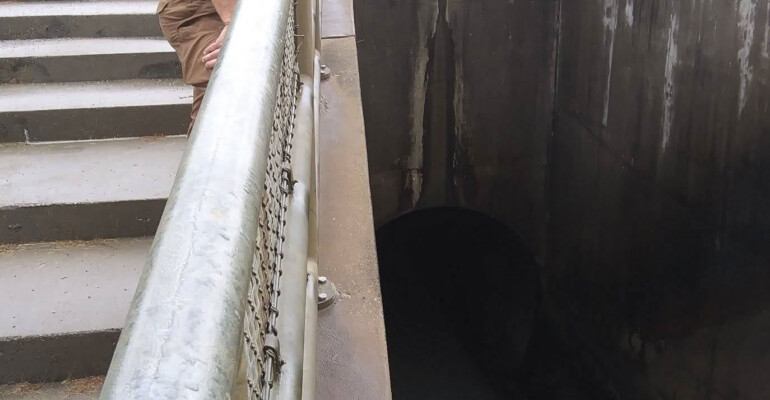
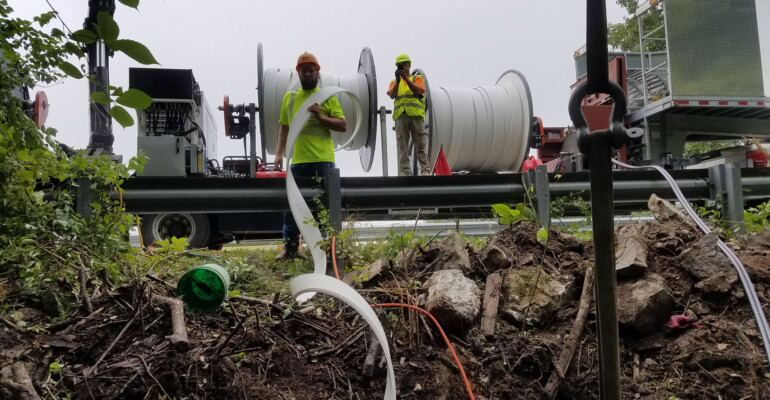

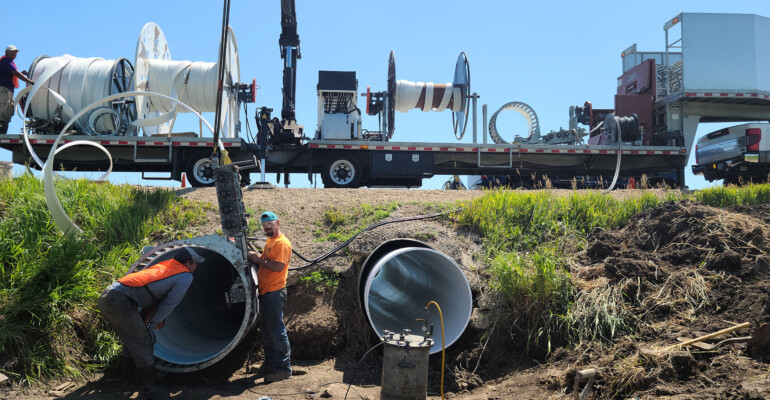
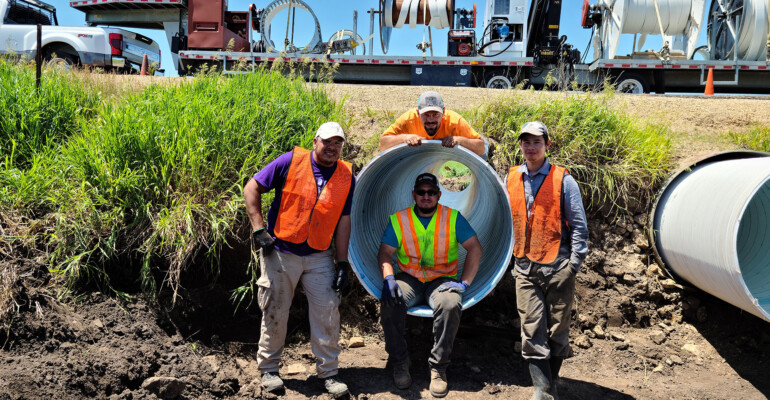
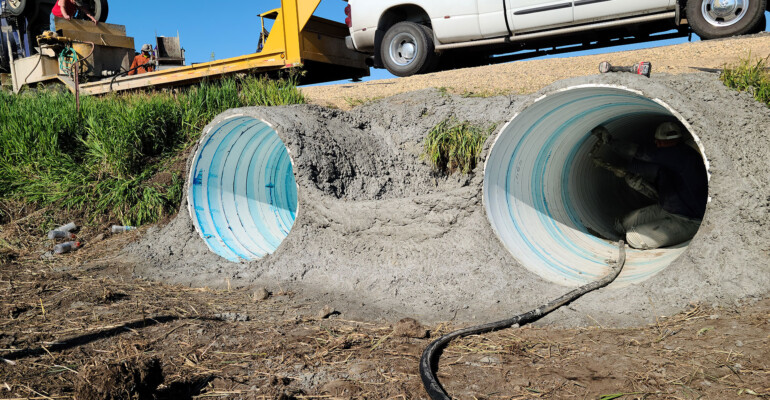
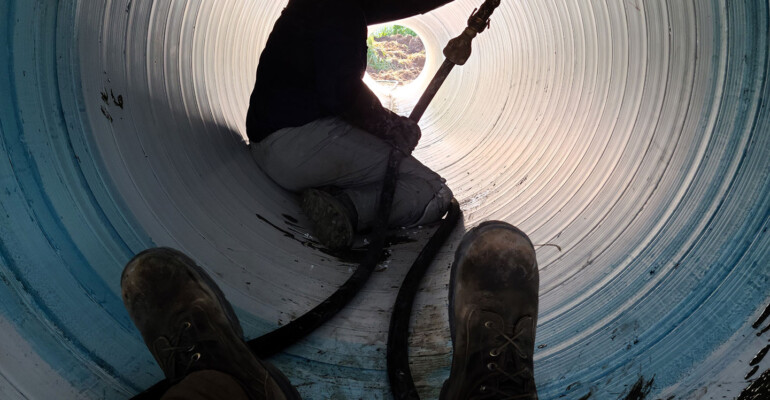
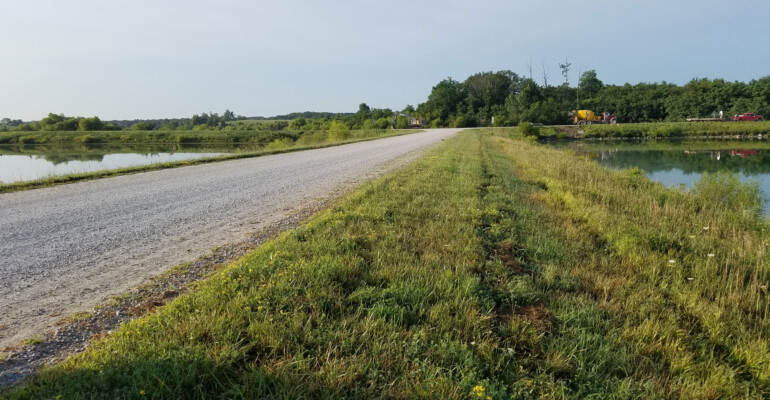
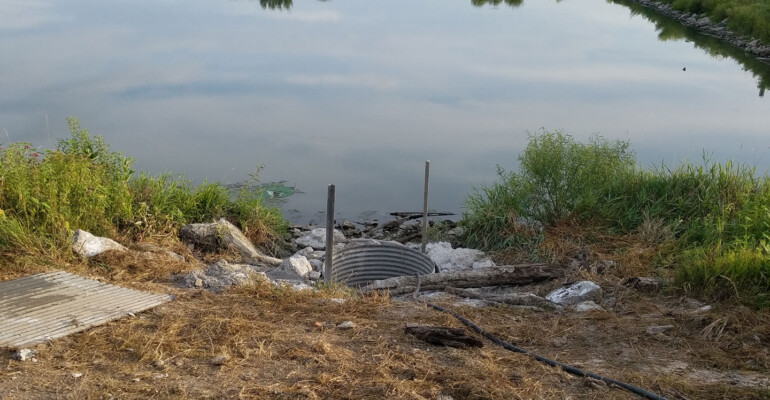
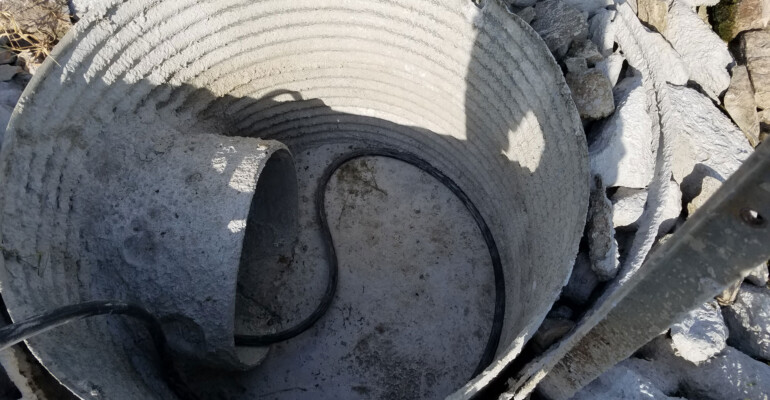
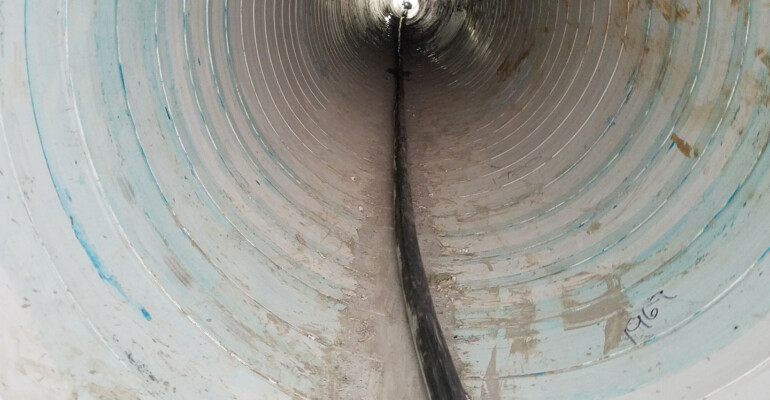
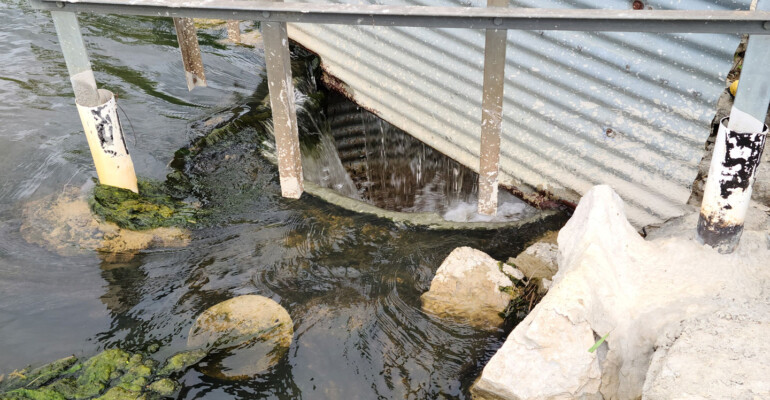
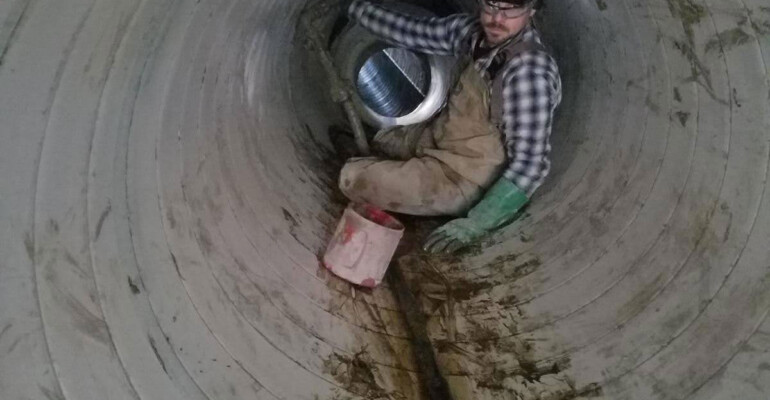
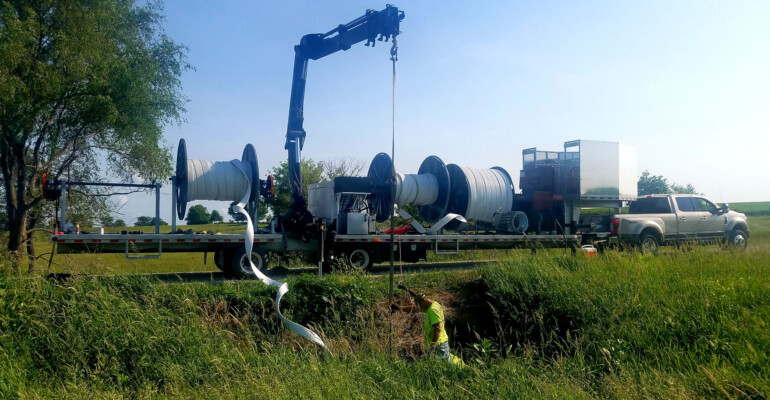
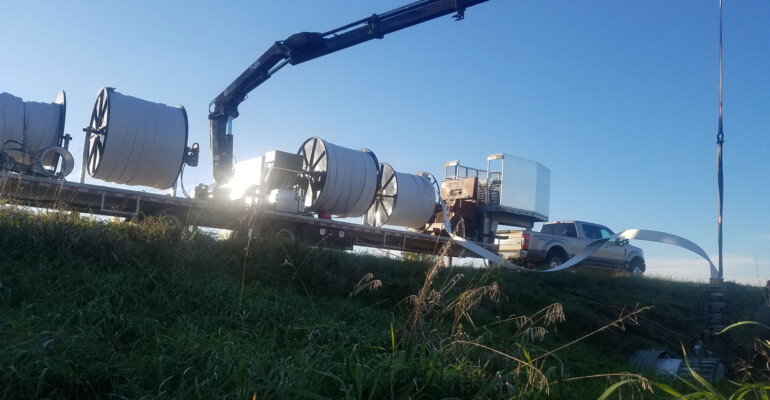
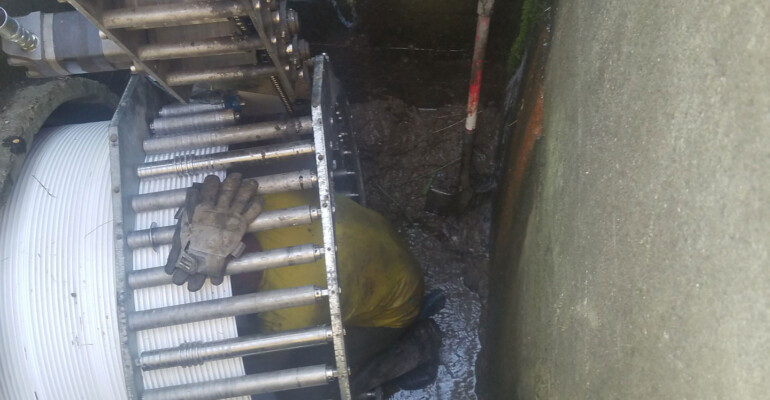